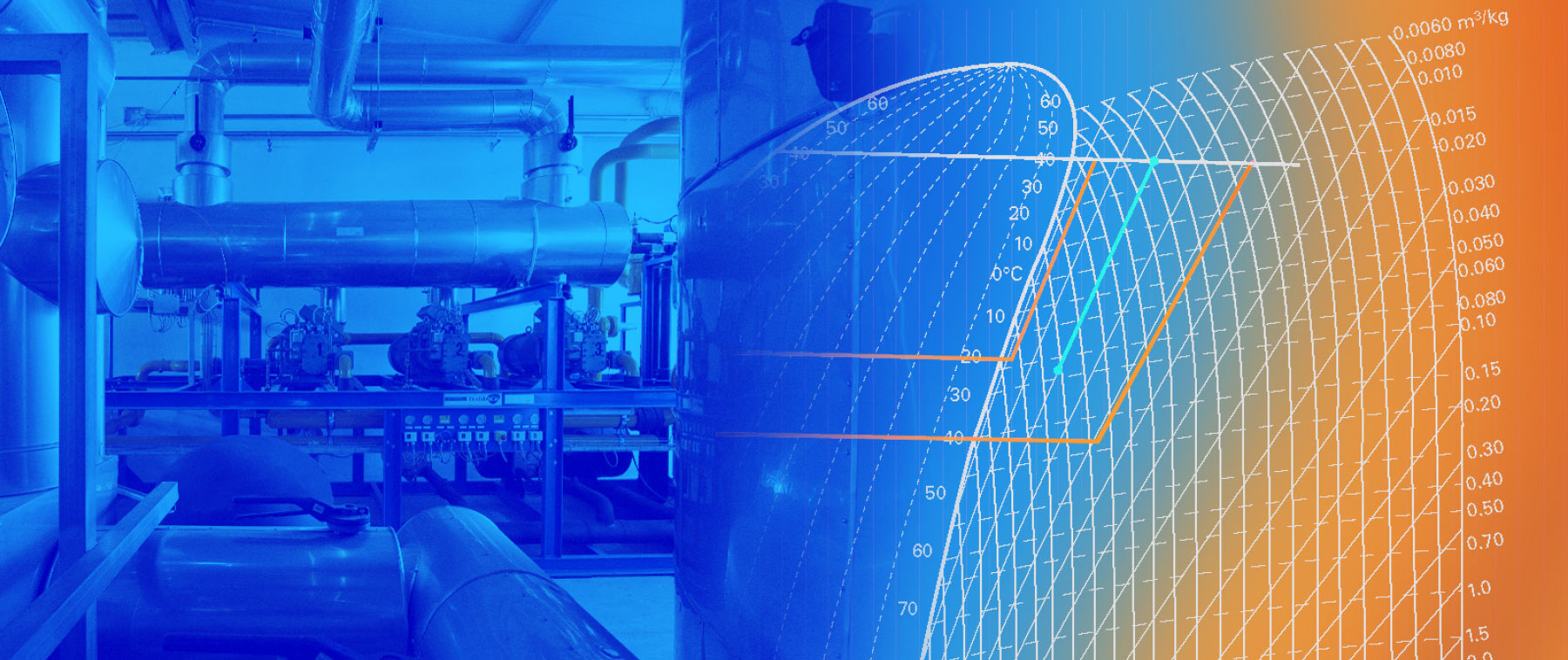
Refrigeration plants
Top performance with the
lowest power consumption

Refrigeration units
We project and build NT (Normal Temperature) , LT (Low Temperature) and XLT refrigeration units; working with Freon or ammonia or carbon dioxide; direct expansion (DX) type or working with a secondary fluid (chillers). The units can be installed indoors with a remote condenser or outdoors with housing and condenser on board. Compressors can be reciprocating or screw type, connected in parallel and fitted with an electric motor coupled with an inverter to increase energy efficiency, even at partial load operation.
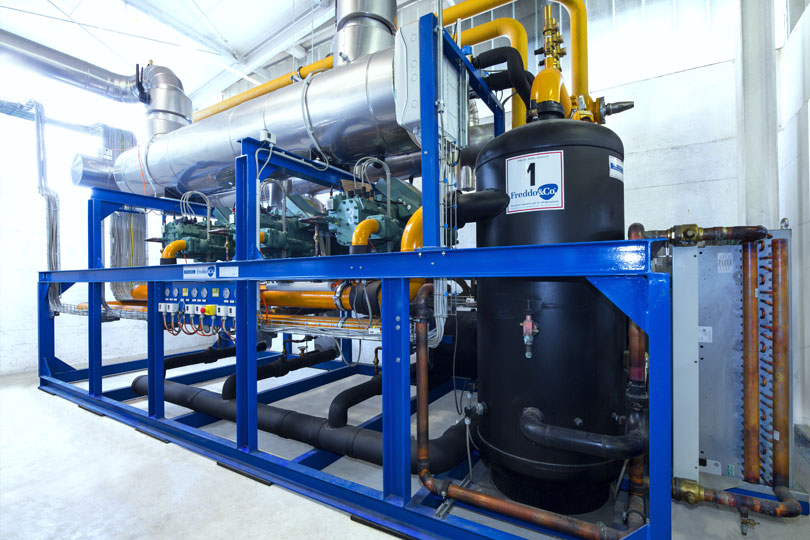

Condensers
We manufacture several types of condensers, according to the project requirements. Our production range includes water- cooled condensers, air-cooled condensers or mixed water/air-cooled condensers. The condensers are generously sized to meet the customer’s needs in terms of operation and energy saving.
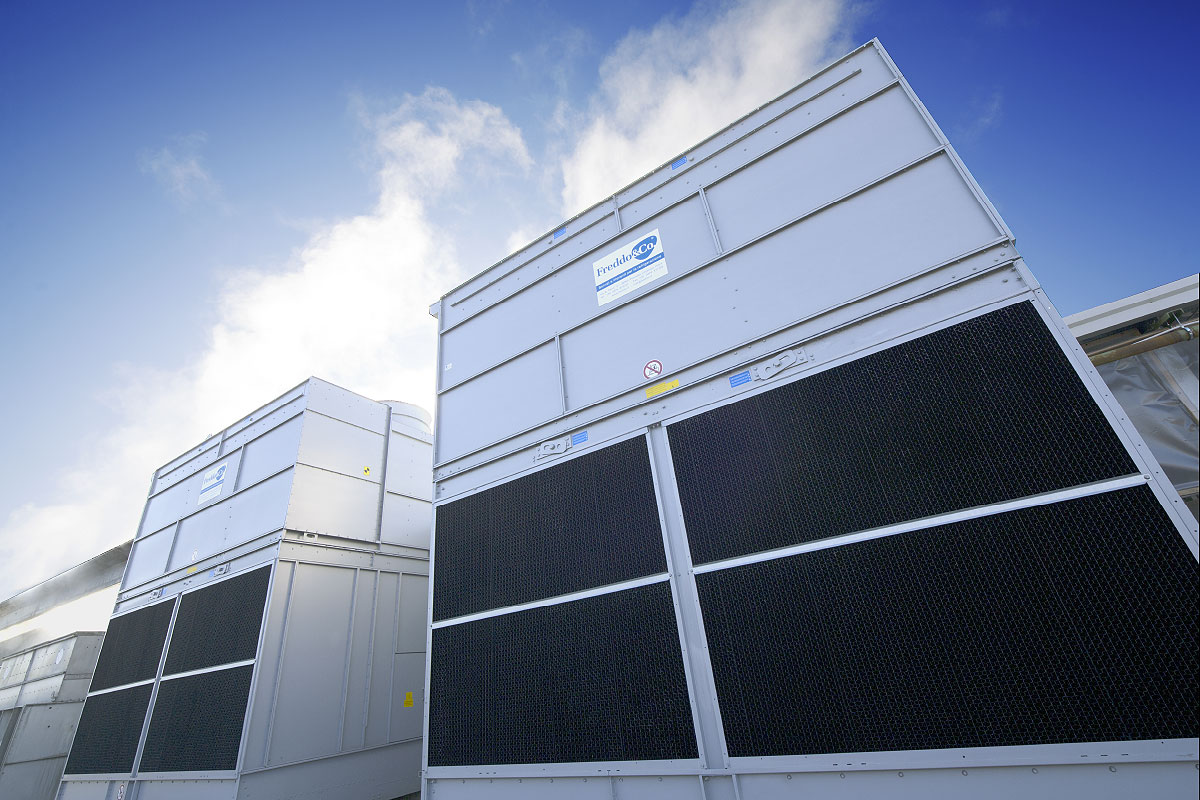
Tower or well water-cooled (shell and tube/plate): they are projected for limiting the condensing pressure especially in summer and reducing the load of refrigerant;
Air-cooled (fan-cooled battery): easily inspectable with low operating and maintenance costs;
Mixed water and air-cooled (evaporative): used for medium-to-large sized industrial plants to optimize thermal/ energy performance throughout the year.
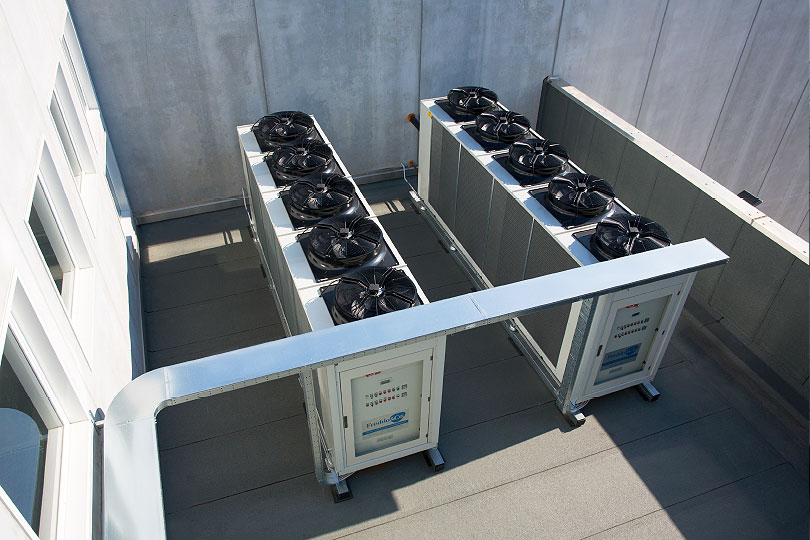

Condensing units
Condensing units are refrigeration units with a built-in air/water condenser, according to the customer’s specific requirements. The air-cooled condenser is equipped with axial fans with inverters. The water-cooled condenser can be either of the shell and tube or plate type, on the base of the size and technical specifications or the design of the unit, as well as the chemical properties of the water running in the heat exchangers.

Evaporators
Evaporators can be ventilated air coolers (typically used in cold rooms) and static air coolers (typically used in drying, aging and curing chambers); or with shell and tube/plate for cooling of the secondary fluid (glycol water or brine).
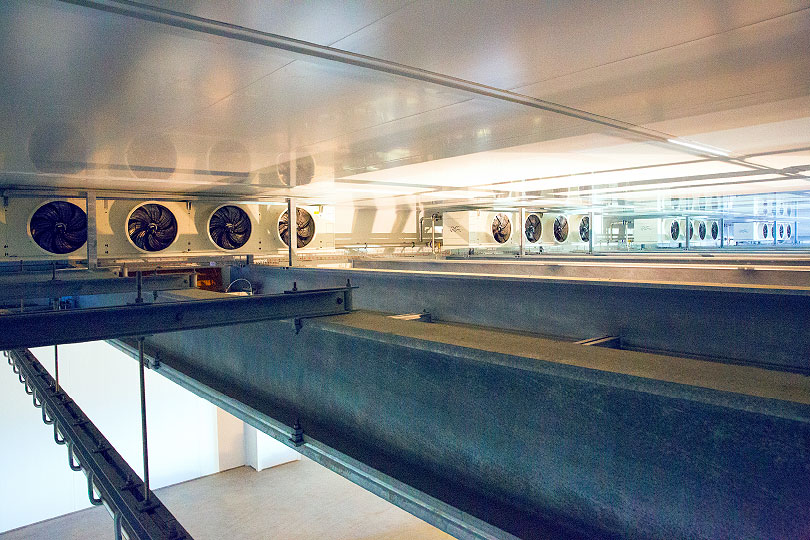

Air-Handling Units
Air Handling Units (AHU) are manufactured in standard or sanitizable version. Standard AHUs are suited for use in working conditions that do not require a high level of sanitation. Sanitizable AHUs are units with a monocoque structure in reinforced fibreglass that provides excellent thermal insulation. The fan in stainless steel is centrifugal type with no volutes, is adjustable with an inverter and is directly coupled with the motor with no drive belt (which is a component that is easily polluted). The heat exchanger coils have copper/stainless steel pipes and aluminium/stainless steel fins, with the option of performing a cataphoretic treatment. AHUs allow customers to maintain the desired thermal conditions in the environment, to filter the air blown into the room, and to ensure proper air circulation to staff on site. Generally, AHUs are equipped with the Free Cooling system to clean the premises, avoiding contamination and component wear and improving energy efficiency.

Ice storage banks
The banks consist of a structure made of sandwich polyurethane-foam panels covered by stainless sheet steel. A containment cover in heat-sealed PVC is installed inside the bank to ensure waterproofness.
The programmed melting of the ice accumulated during the night (when the cost of electricity is lower) ensures cooling of the process water. The special heat exchangers of the storage bank are built in the shape of a coil in order to ensure a continuous melting process and provide added savings.
In the case of a plant with serial banks, their operation can be optimised with our WIAS system.
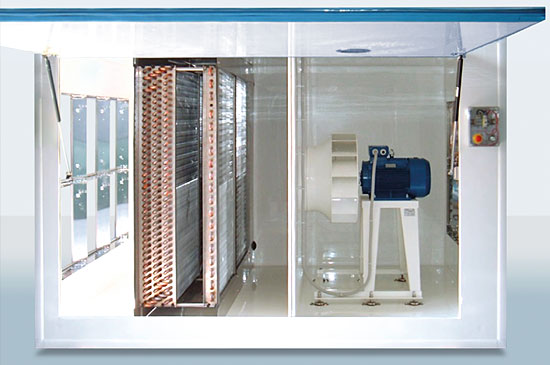
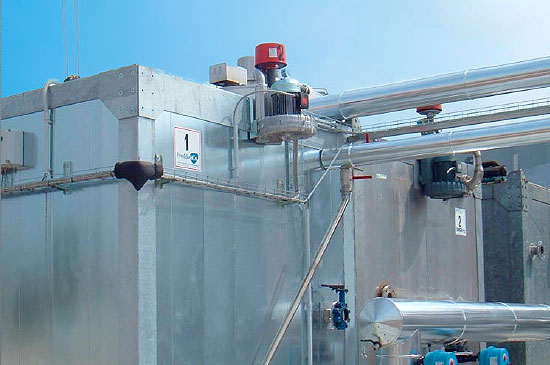

Electrical boards
The cabinet of the electrical boards is wide in order to facilitate service tasks and to leave more space for the installation of any technological components you may need to incorporate. The layout of the electrical boards is designed to meet the requirements of the applicable laws and regulations, avoiding the possibility that technical staff may perform incorrect operations. A programmable logic controller (PLC) is part of all our models, even the less complex ones, in order to automate the processes and improve the quality-to-tech ratio, guaranteeing the best performance in terms of multifunctionality and energy saving.
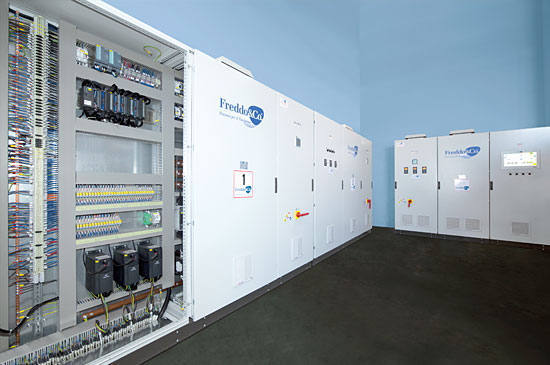
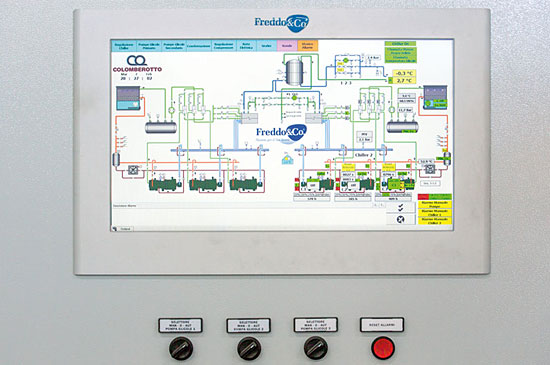

Processing rooms
Providing a safe work environment to staff assigned to the processing of products is the priority for any project engineer when determining the size of an air conditioning plant. The air flow is an important factor, but even more so are the distribution ducts. Micro-perforated polyamide ducts, in fact, ensure non-stratified air temperature.
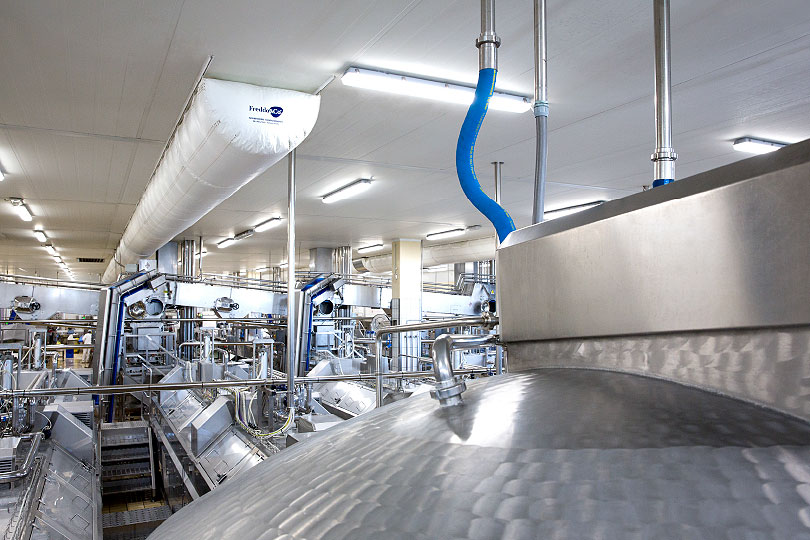
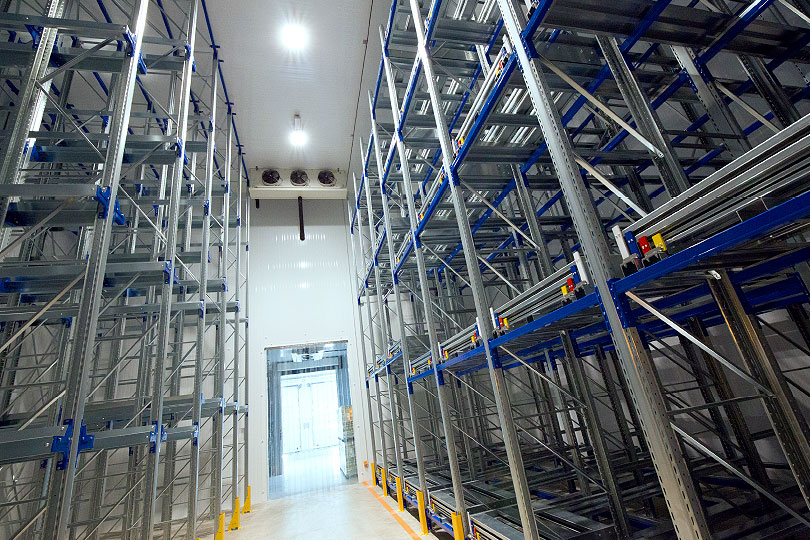

Automated warehouse
Ventilation is essential for refrigerated air to reach all the products stocked. In fact, it is absolutely crucial to avoid any form of stratification and significant temperature differences. To avoid these problems, the evaporators manufactured by Freddo&Co. are sized to provide an adequate air flow and air throw to reach all the areas.

Cold rooms
Cold rooms are projected to store any type of product while complying with very strict heat and humidity parameters, in order to preserve the cold chain.
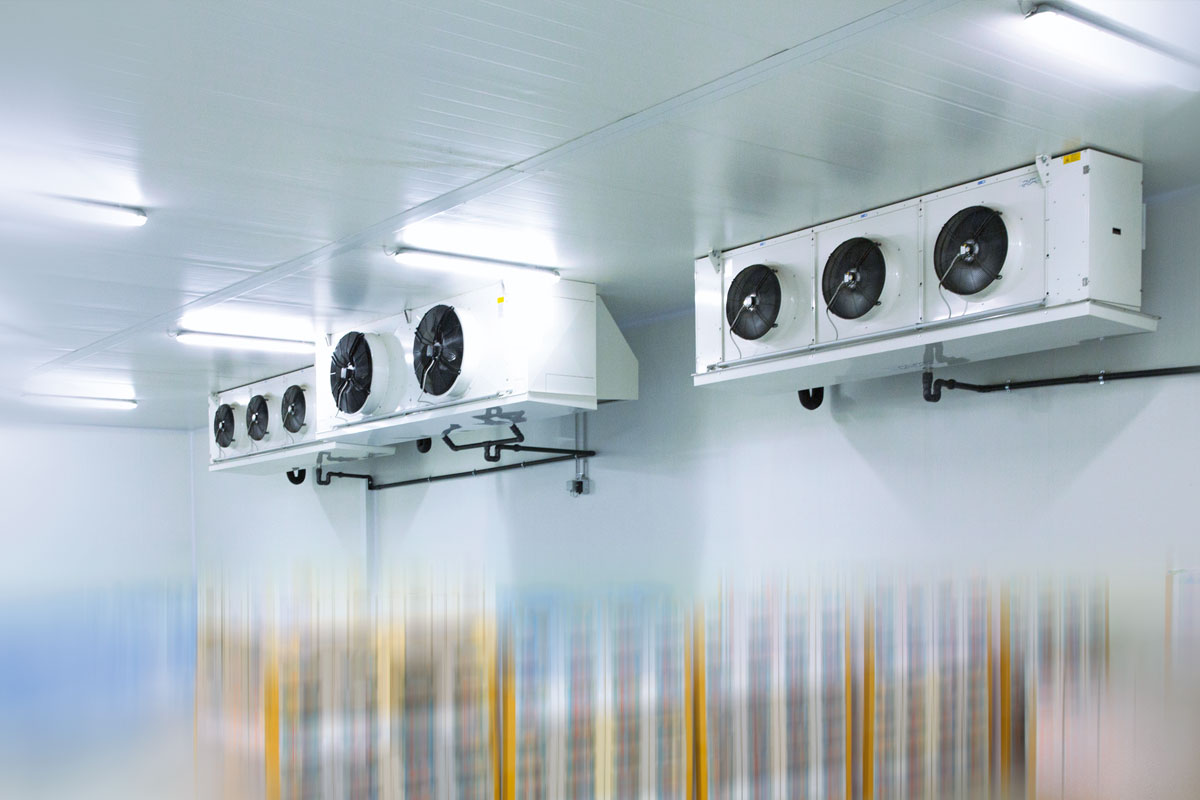
They are made of modular isothermal sandwich panels with a finish in pre-coated steel sheet and insulation in polyurethane foam of various thickness, and have strong doors projected to meet logistic needs. Besides cold rooms for the storage of products, Freddo&Co. also manufactures drying and aging/curing chambers for cheese/salami/meat; rooms with a controlled atmosphere for fruits and vegetables; heating chambers for dairy products; low-temperature cold rooms; blast cooling rooms and tunnels; freezing tunnels; deep-freezing tunnels.
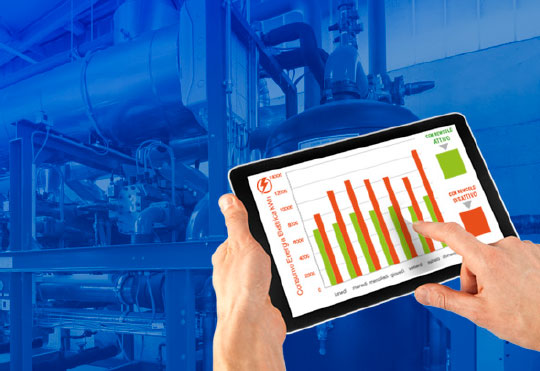
NewCold System
reduce the energy costs
of your refrigeration plant
from 10 to 30%
The NewCold System is the revolutionary energy-saving system by Freddo&Co. that can be installed both on new plants and existing ones of the most popular brands. The actual savings achieved thanks to the NewCold System can be tested and proven before installation.
READ MORE